Explore the versatility of plastic extrusion in design
A Comprehensive Overview to the Process and Benefits of Plastic Extrusion
In the huge world of production, plastic extrusion arises as a vital and very effective process. Translating raw plastic right into continual accounts, it provides to a huge selection of sectors with its remarkable adaptability.
Recognizing the Basics of Plastic Extrusion
While it might appear complex at first glance, the process of plastic extrusion is essentially easy. The process starts with the feeding of plastic product, in the type of powders, granules, or pellets, into a heated barrel. The designed plastic is after that cooled, solidified, and reduced right into preferred lengths, finishing the procedure.
The Technical Refine of Plastic Extrusion Explained
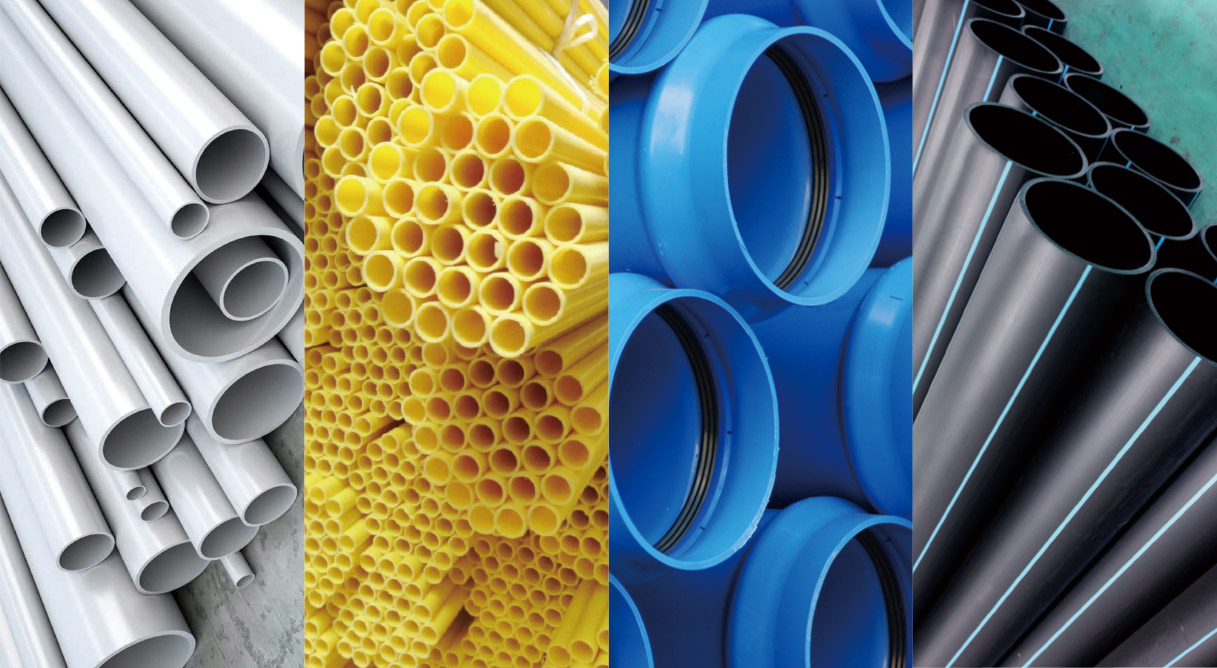
Kinds Of Plastic Suitable for Extrusion
The option of the appropriate type of plastic is an essential element of the extrusion process. Different plastics provide distinct properties, making them a lot more suited to certain applications. Recognizing these plastic types can dramatically enhance the extrusion procedure.
Comparing Plastic Extrusion to Other Plastic Forming Approaches
Understanding the kinds of plastic ideal for extrusion leads the way for a more comprehensive conversation on exactly how plastic extrusion compares to other plastic developing approaches. These consist of shot molding, strike molding, and thermoforming. Each method has its unique usages and advantages. Shot molding, for example, is superb for developing elaborate components, while strike molding is excellent for hollow things like bottles. Thermoforming excels at forming large or shallow parts. However, plastic extrusion is unrivaled when it comes to producing continuous accounts, such as pipes, gaskets, and seals. It likewise enables a constant cross-section along the size of the item. Thus, the option of method mostly depends upon the end-product needs and requirements.
Key Advantages of Plastic Extrusion in Manufacturing
In the world of manufacturing, plastic extrusion supplies many substantial benefits. One noteworthy advantage is the cost-effectiveness of the process, that makes it an economically attractive manufacturing method. In addition, this technique gives remarkable product flexibility and enhanced manufacturing rate, thereby increasing general manufacturing performance.
Cost-efficient Production Approach
Plastic extrusion jumps to the center as an affordable manufacturing approach in manufacturing. In addition, plastic extrusion needs less power than conventional production techniques, contributing to reduced operational costs. Overall, the financial benefits make plastic extrusion an extremely appealing choice in the production industry.
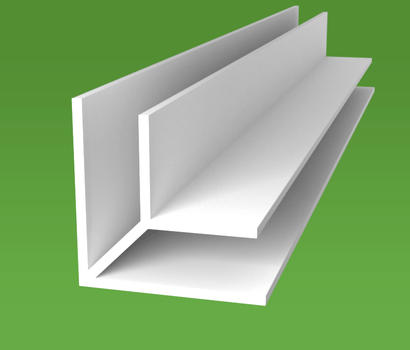
Superior Item Adaptability
Past the cost-effectiveness of plastic extrusion, another substantial benefit in manufacturing hinge on its superior product versatility. This procedure allows for the production of a vast variety of products with differing layouts, important site forms, and dimensions, from simple plastic sheets to complex profiles. The adaptability is credited to the extrusion die, which can be personalized to produce the desired product design. This makes plastic extrusion a perfect option for sectors that require personalized plastic elements, such as automobile, building, and packaging. The capacity to generate varied products is not just beneficial in meeting certain market demands however also in enabling suppliers to explore new item lines with minimal resources investment. Essentially, plastic extrusion's product versatility fosters technology while boosting functional performance.
Enhanced Production Speed
A significant benefit of plastic extrusion exists in its improved manufacturing speed. Couple of various other manufacturing procedures can match the speed of plastic extrusion. In addition, the ability Full Report to keep regular high-speed manufacturing without giving up product quality sets plastic extrusion apart from other methods.
Real-world Applications and Impacts of Plastic Extrusion
In the realm of production, the method of plastic extrusion holds profound significance. The economic advantage of plastic extrusion, mostly its high-volume and cost-efficient result, has company website changed production. The sector is constantly making every effort for advancements in eco-friendly and recyclable products, showing a future where the benefits of plastic extrusion can be maintained without compromising environmental sustainability.
Verdict
To conclude, plastic extrusion is a extremely efficient and effective technique of transforming raw products into varied items. It offers various benefits over various other plastic creating methods, consisting of cost-effectiveness, high output, minimal waste, and design versatility. Its impact is exceptionally felt in various industries such as building and construction, automobile, and durable goods, making it a critical procedure in today's production landscape.
Diving much deeper into the technological procedure of plastic extrusion, it begins with the choice of the ideal plastic product. As soon as cooled, the plastic is cut into the needed sizes or wound onto reels if the product is a plastic movie or sheet - plastic extrusion. Comparing Plastic Extrusion to Other Plastic Forming Techniques
Understanding the types of plastic suitable for extrusion paves the means for a more comprehensive conversation on just how plastic extrusion piles up against other plastic creating techniques. Few various other production processes can match the rate of plastic extrusion.